Co-authored and reviewed by Business & Digital Marketing Expert Guy Shapira.
A Guide to Quality Improvement Learning Collaborative Technical Assistance
Quality improvement (QI) is pivotal in transforming businesses, healthcare systems, and organizations into more efficient and effective entities. Over my years of coaching business leaders, healthcare administrators, and aspiring executives, I’ve seen firsthand how well-designed quality improvement processes can deliver meaningful change. One strategy I particularly recommend is Quality Improvement Learning Collaborative Technical Assistance.
Hi. I’m Ryan Zofay, a founder of the We Level Up Behaviroal Health Treatment Centers, a nine-figure organization. Over the years I’ve dedicated thousands of hours of study to gain the skills to drive meaningful personal growth through quality improvement learning collaborative technical assistance for businesses. Through my seminars and practices, I’m committed to showing leaders how to drive success, innovation, and—most importantly—continuous quality improvement.
My personal experience with quality improvement learning collaborative technical assistance initiatives
My personal Guide to Driving Success in a quality improvement learning collaborative
Hi, I’m Ryan Zofay—a business coach, entrepreneur, and someone who’s spent years helping individuals and teams unlock their potential. Whether you’re a seasoned business leader or part of a quality improvement team looking for that next breakthrough, you’re probably wondering how to elevate your outcomes and how quality improvement learning collaborative technical assistance can help you gain effectiveness and productivity.
Success doesn’t happen by chance—it’s built step by step through structured planning, execution, and a commitment to continuous improvement. That ethos lies at the core of my seminars and business practices, which have helped countless professionals turn their challenges into opportunities for lasting success. I’ll cover and show you how to implement proven strategies for quality improvement learning collaborative technical assistance with clarity, confidence, and impact.
What is a Quality Improvement Learning Collaborative?
First, the basics. A quality improvement learning collaborative (QILC) is a structured yet dynamic approach for teams or organizations to share best practices, analyze performance data, and implement strategies that lead to tangible improvements. These collaboratives often include workshops, interactive sessions, expert-led seminars, and one-on-one technical assistance to foster innovation and collaboration.
Sound complex? Don’t worry—it’s easier to break down and implement when approached strategically.
Why Quality Improvement Matters
If you’re here, you know why improvement matters. Businesses thrive on the ability to adapt, implement better processes, and ultimately produce higher-quality products or services that customers rave about. This is where quality improvement plans and actions come into play. A solid quality improvement plan example can serve as a roadmap to help your team elevate everything from how you improve production quality to how you enhance data reliability.
But quality isn’t just about numbers. It’s about empowering individuals and teams to take ownership of their work, align with your strategic vision, and celebrate big and small wins together.
My Personal Approach to Quality Improvement
What sets my strategy apart is that I focus on the human element. Through my seminars, I guide teams to shift their perspective, work collaboratively, and build processes that are as people-focused as they are results-driven.
Here’s how I approach quality improvement initiatives in a way that realigns not just a team but the people within it:
Step 1. Paint the Vision
Every transformation starts with a destination in mind. A clearly defined goal or quality improvement plan sample helps teams move with intent. But here’s the catch—your “why” matters just as much as your “what.” Your motivation has to resonate with everyone involved.
Ask yourself and your team:
- How will this improve the quality of our work?
- How will it benefit our clients or customers?
- How does this align with our mission/values?
Step 2. Foster Collaboration
Remember, it’s a learning collaborative for a reason. Quality improvement thrives on the back-and-forth exchange of successful strategies, lessons learned, and technical assistance from leaders in the field.
Make space for your team to:
- Share what’s working (and what isn’t).
- Network with other professionals tackling similar challenges.
- Use data to guide conversations and decisions. (Pro tip: Focus discussions on examples like how to improve data quality or streamline specific processes.)
Step 3. Execute Bite-by-Bite
Empowering teams to take control of quality and process improvement doesn’t happen in one big push. Break down your vision into implementable steps. Start small, nail it, and build on that success.
For instance, maybe your first focus is learning how to improve product quality without overhauling your entire production system. Prioritize one product line and test a strategy. Evaluate, adjust, and repeat.
Step 4. Measure Everything That Matters
Goals without data are just ideas. Incorporating systems like QSEN quality improvement principles or metrics from a quality improvement plan example ensures your efforts are measurable and trackable.
Ask:
- Are we hitting our quality improvement (QI) benchmarks?
- Are there measurable gains in production? (e.g., have we improved product quality metrics?)
- Are customers/users responding positively? (e.g., improved satisfaction scores, fewer complaints.)
Step 5. Commit to Continuous Improvement
One of my favorite teachings is that improvement isn’t a box to check off—it’s a cycle. Your initial success is just the beginning. Leverage that momentum to create a rhythm of quality and continuous improvement.
At regular intervals, ask:
- What can we refine further?
- What challenges have emerged since our last QI cycle?
- What’s preventing our next big leap forward?
Step 6. Celebrate Successes
Quality improvement is hard work, and progress is not always linear. By taking the time to acknowledge milestones, no matter how small, you encourage your team to stay engaged and motivated. This is central to quality improvement learning collaborative technical assistance—keeping people invested in the process and proud of their contributions.
Practical Application Examples
If you seek to improve product quality or improve production quality begin by learning how to create a business case for data quality improvement.
Pick your sample quality improvement project and begin a continuous quality improvement process through a well-thought-out quality improvement plan.
- For Businesses: Implementing a team-wide quality improvement plan to reduce errors in product manufacturing by X%.
- For entrepreneurs: Using my seminars to learn techniques for improving customer trust by maximizing service quality.
- For Quality Improvement Teams: Applying frameworks to tackle challenges like how to improve customer satisfaction scores through reliable data analysis.
Why choose my quality improvement learning collaborative technical assistance Approach
Over the years, I’ve helped countless individuals and companies tackle large-scale quality improvement challenges. What inspires me is seeing tangible change—increased confidence, meaningful growth, and processes that genuinely make a difference.
You’ll come for the technical assistance, but you’ll stay because of the curiosity and camaraderie you foster within yourself and your team. Together, we’ll learn, implement, grow—and, yes, celebrate!
Are you ready to Transform?
Don’t settle for average or “we’ve always done it this way” complacency. Whether leading a business, managing a department, or working individually, success in quality improvement learning collaboratives is within your reach.
Want direct insight into how I help businesses achieve this? Join one of my seminars or explore personalized strategies through a 1-on-1. You won’t just learn how to improve product quality or kickstart a quality improvement plan—you’ll build a mindset equipped to tackle challenges with clarity and confidence.
Get started today.
Jump To
Table of Contents
Boost performance with quality improvement learning collaborative technical assistance Plans
I’ll explain what a Quality Improvement Learning Collaborative is and how it works, and provide practical how-tos, strategies, insights, and advice that will help to improve effectiveness in your own organization.
Whether you’re a healthcare administrator wanting to improve patient care or an executive seeking operational excellence, this guide will provide actionable insights you can implement today to improve effectiveness through quality improvement learning collaborative technical assistance projects.
Understanding a Quality Improvement Learning Collaborative
You may have heard the term “Quality Improvement Learning Collaborative (QILC)” tossed around. But what does quality improvement learning collaborative technical assistance mean, and how can it benefit you, your team, or your organization? Allow me to break down the implications and process of quality improvement learning collaborative technical assistance. I’ll guide you through the advantages—and show how these methods can spark meaningful change.
What is a Quality Improvement Learning Collaborative?
Put simply, a Quality Improvement (QI) Learning Collaborative is a structured, team-based approach where organizations work together to learn, share, and implement best practices for quality improvement. Guided by experts, this collaborative model fosters collective problem-solving and measurable results.
Participants work on shared goals but also benefit from tackling individual organizational challenges. For instance, healthcare organizations might collaborate to improve patient outcomes or streamline processes. Business leaders in other industries might focus on enhanced efficiency, product quality, or customer satisfaction.
Key features of a QI Learning Collaborative include:
- Knowledge Sharing: Teams exchange real-life lessons and best practices.
- Expert Technical Assistance: Facilitators coach teams on QI methodologies such as Plan-Do-Study-Act (PDSA) cycles.
- Data-Informed Decision Making: Success is measured by data-driven outcomes.
- Collaborative Goal Setting: Participants define improvement targets collectively and hold one another accountable.
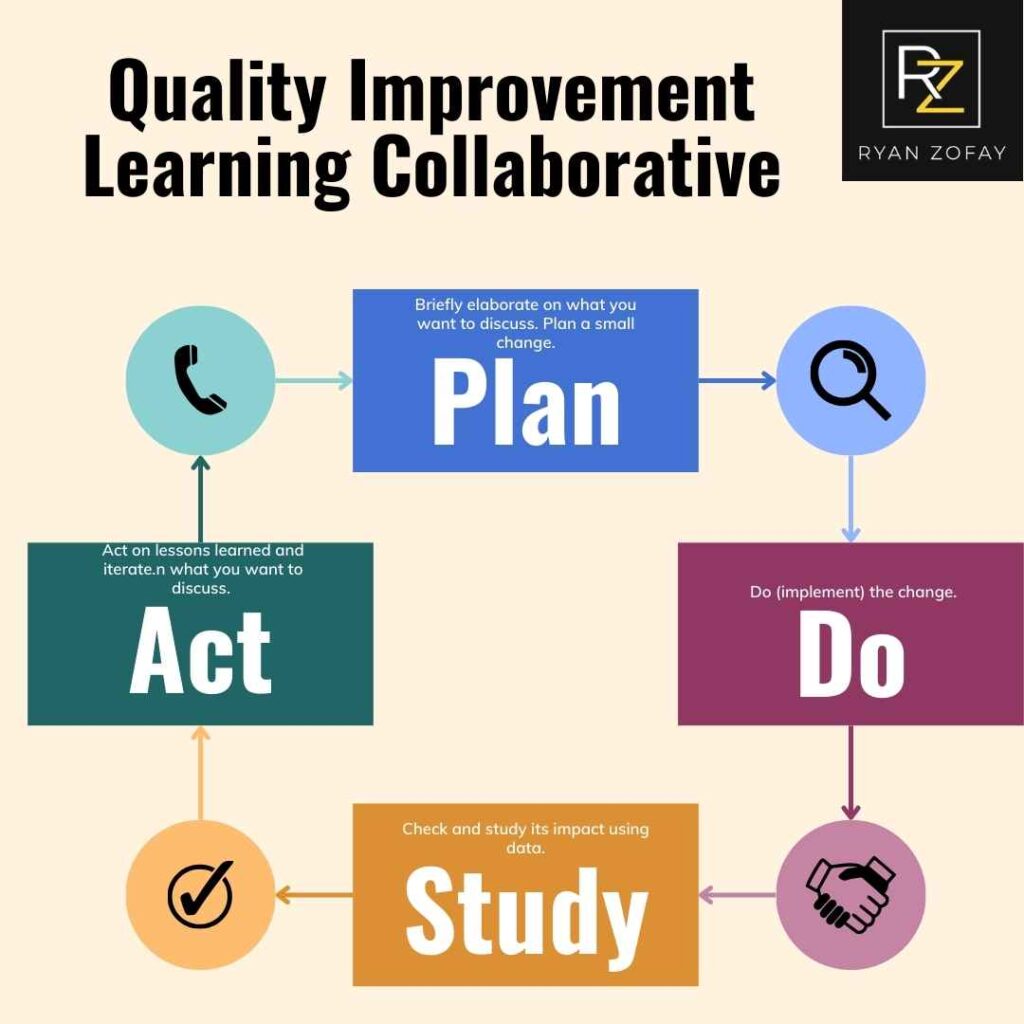
The outcomes? Improved quality, optimized processes, and a shared sense of achievement across teams.
The 4 Categories of Quality Improvement
Effective QI collaboratives operate on these four key pillars:
- Patient Outcomes (or Customer Satisfaction for non-healthcare industries): The focus is always on delivering improved results that matter most to end-users.
- Process Improvements: Streamlining tasks for better efficiency and fewer errors.
- Staff Engagement: Ensuring those executing the processes feel empowered and informed to enact meaningful change.
- Cost Efficiency: Reducing waste and associated costs while maintaining high standards.
When these four elements align, the results speak for themselves. Whether managing a healthcare facility or running a business, framing your efforts around these categories sets you up for success.
The 5 Components of Quality Improvement
To successfully run a QI Learning Collaborative, there are five components every participant organization must master:
- Clear Goals: Clearly defined outcomes are essential. Without them, a QI project risks lacking focus and accountability.
- Engaged Leadership: Executive buy-in is crucial to driving collaboration and securing resources.
- Reliable Data: Collect meaningful metrics to assess progress and direct future actions.
- Consistent Training: Equip your team with knowledge of continuous quality improvement processes, PDSA cycles, and other tools. The continuous quality improvement process is designed to systematically enhance an organization’s processes, products, or services.
- Sustainability Planning: Build procedures into everyday practice so improvements last.
These quality improvement learning collaborative technical assistance principles remind me of launching initiatives at the We Level Up Behavioral Health Centers. With the right framework, even the most ambitious goals are achievable.
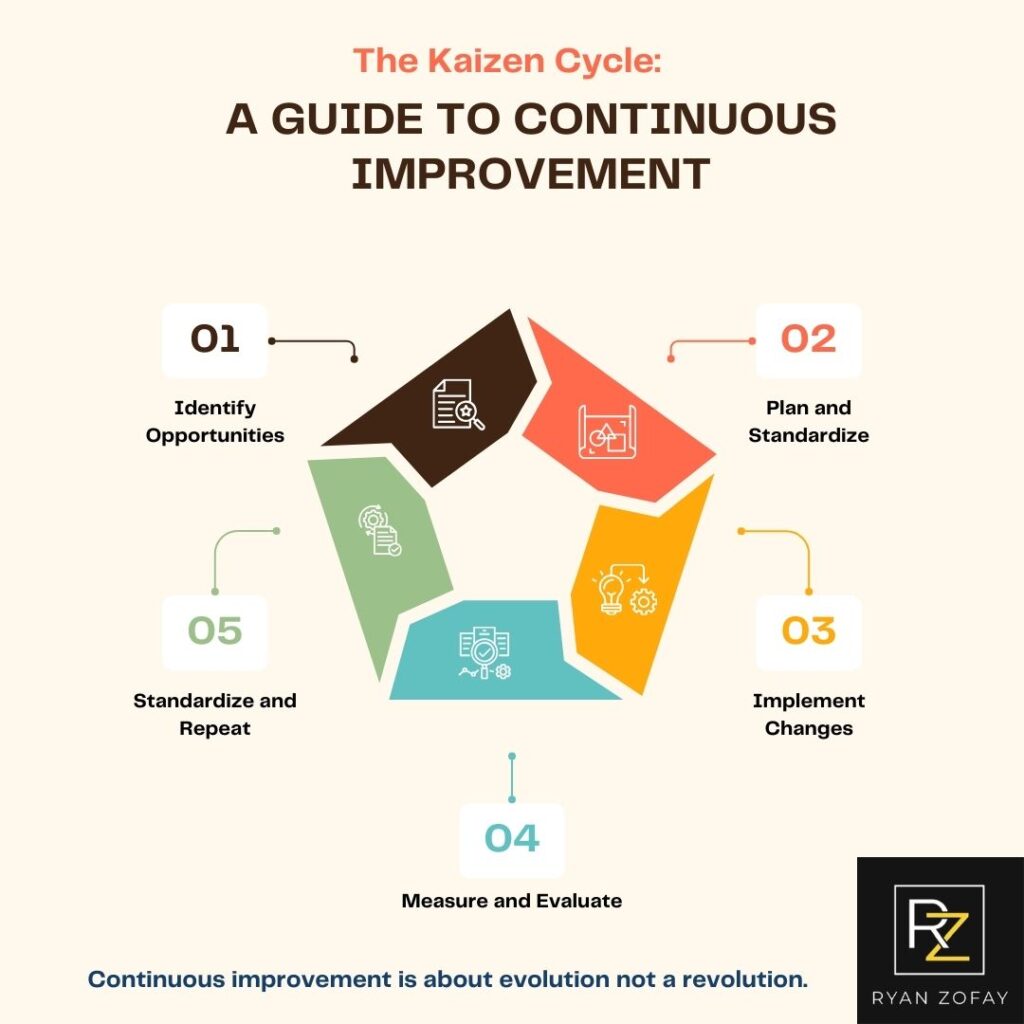
How to Launch a Successful Quality Improvement Learning Collaborative Technical Assistance Project
Launching a quality improvement learning collaborative technical assistance or QI project doesn’t have to be overwhelming if you follow these five steps:
Step 1. Assemble a Team
Bring together key staff from across your organization, focusing on people with diverse expertise and perspectives. For larger collaboratives, invite external organizations to participate.
Step 2. Define Clear Objectives
Ask yourself, “What kind of ‘improved quality’ do we want to achieve?” Be specific with metrics or outcomes—this is your North Star throughout the project.
Step 3. Use Data to Diagnose Problems
Data plays an invaluable role in identifying opportunities for improvement. Use tools like root cause analyses to address underlying challenges instead of symptoms.
Step 4. Implement the PDSA Cycle
The PDSA cycle—Plan, Do, Study, Act—is a hallmark framework for trialing improvements:
- Plan a small change.
- Do (implement) the change.
- Study its impact using data.
- Act on lessons learned and iterate.
It’s iterative, so your team can test ideas without fully committing to risky, large-scale changes.
Step 5. Foster Collaboration
Tap into your organization’s peer organizations, industry leaders, or even cross-functional teams. Collaborative learning creates accountability and exposes participants to new ideas.
Adopting a commitment to continuous quality improvement not only ensures the success of your current initiatives but also helps prepare your organization to tackle future challenges and opportunities.
Implement a premium assessment and quality improvement strategy
Implementing a Premium Assessment and Quality Improvement strategy is essential for organizations aiming to enhance performance, ensure compliance, and deliver superior services. This approach involves a comprehensive evaluation of current processes, identification of improvement areas, and the application of structured methodologies to achieve measurable enhancements.
Alright, here’s a bullet-point breakdown of how to implement a premium assessment and quality improvement strategy, based on my experiences:
- Dive Deep into Your Processes:
- Conduct a thorough analysis of all operational aspects.
- Identify inefficiencies and areas needing improvement firsthand.
- Invest in Staff Education:
- Keep your team updated on regulations and compliance.
- Empower them with the skills for effective quality improvement.
- HR and Compliance:
- Ensure all personnel files are in order and up-to-date.
- Verify credentials to avoid potential legal issues.
- Implement PDSA Cycle:
- Make small, manageable changes.
- Evaluate results and scale up successful strategies.
- Monitor Progress with KPIs:
- Establish key performance indicators for tracking.
- Conduct regular check-ins to address issues promptly.
- Cultivate a Continuous Improvement Mindset:
- Encourage all team members to seek ways to improve.
- Promote a culture of excellence at every level.
- Focus on Customer Satisfaction:
- Ensure all improvements ultimately benefit the customer.
- Prioritize customer satisfaction as a core objective.
- Commitment and Focus:
- Stay committed to the process, even when it’s challenging.
- Maintain a focus on continuous improvement and excellence.
Continuous Quality Improvement (CQI)
The Continuous Quality Improvement (CQI) process is designed to systematically enhance an organization’s processes, products, or services. Rooted in the belief that there is always room for improvement, CQI encourages a culture of ongoing assessment and refinement.
Here’s the breakdown of Continuous Quality Improvement (CQI) from my experiences as a leader, businessman, and business coaching pro:
- Constant Evolution is Key:
- Always strive for improvement; never settle for the status quo.
- Embrace change and view it as an opportunity for growth.
- Enhance Performance and Efficiency:
- Streamline processes to work smarter, not harder.
- Regularly evaluate operations and make necessary adjustments.
- Prioritize Customer Satisfaction:
- Proactively identify and address issues impacting customer experience.
- Exceed customer expectations to build loyalty and advocacy.
- Foster a Culture of Continuous Improvement:
- Encourage all team members to contribute ideas for enhancement.
- Promote a sense of ownership and collaboration.
- Reduce Waste and Costs:
- Identify and eliminate non-value-added activities.
- Optimize resource allocation to improve the bottom line.
- Proactive Strategy is Essential:
- Please don’t wait for problems; anticipate and prevent them.
- Regularly assess operations and encourage feedback.
- Commitment to Progress, Not Perfection:
- Focus on constant forward movement, not unattainable ideals.
- Celebrate small wins and learn from setbacks.
- Transform, Don’t Just Improve:
- CQI is more than just tweaking processes; it’s about reshaping your organization.
- Aim for transformative changes that drive long-term success.
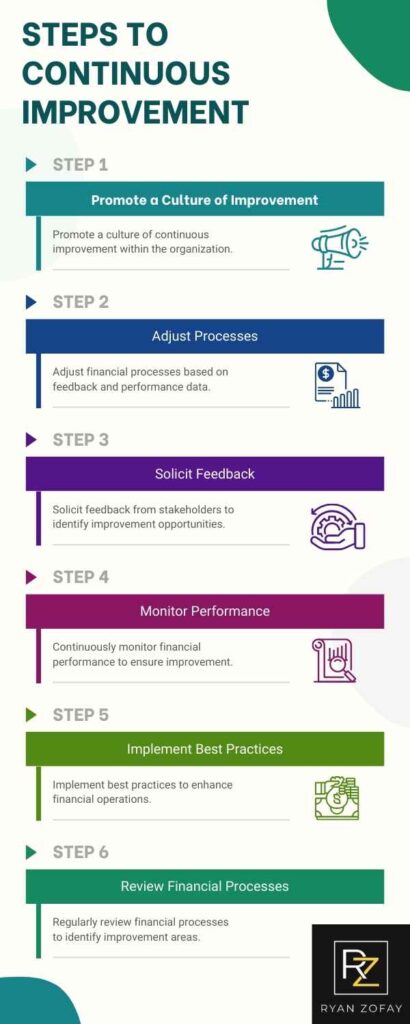
By adopting a structured and comprehensive approach to quality assessment and improvement, organizations can significantly enhance service delivery, compliance, and overall performance.
Quality Improvement Plan Examples
Quality improvement plans (QIPs) are essential for organizations striving to enhance their processes, products, or services. Whether in healthcare, manufacturing, education, or any other industry, a well-designed QIP can help you identify areas for improvement, implement effective solutions, and achieve measurable results.
As a quality improvement expert, I’ve worked with numerous organizations to develop and execute QIPs that drive success. In this guide, I’ll share examples of quality improvement plans across different industries and insights on how to create and implement your own QIP.
What is a Quality Improvement Plan (QIP)?
A Quality Improvement Plan is a structured approach to identifying, analyzing, and addressing areas for improvement within an organization. It typically includes:
- Goals: Clear objectives for improvement.
- Metrics: Key performance indicators (KPIs) to measure progress.
- Actions: Specific steps to achieve the goals.
- Timeline: A schedule for implementation and review.
- Stakeholders: Team members responsible for executing the plan.
quality improvement plan sample insights & Recommendations
Quality improvement plans are not one-size-fits-all; they must be tailored to the specific needs and goals of your organization. Here are some key insights to keep in mind when developing and implementing a QIP:
- Set Clear Goals: Define specific, measurable, achievable, relevant, and time-bound (SMART) goals to guide your efforts.
- Use Data-Driven Decisions: Collect and analyze data to identify areas for improvement and track progress.
- Engage Stakeholders: Involve team members at all levels to ensure buy-in and collaboration.
- Focus on Continuous Improvement: A QIP is not a one-time effort but an ongoing process of refinement and growth.
- Leverage Technology: Tools like automation, data analytics, and feedback systems can enhance the effectiveness of your QIP.
Chart of The Top 7 Quality Improvement Plan Examples & Industries
A well-executed Quality Improvement Plan can transform your organization by driving efficiency, enhancing customer satisfaction, and achieving measurable results. Whether in healthcare, manufacturing, education, or any other industry, the examples and insights in this guide can help you start your journey to continuous improvement.
Industry | Example QIP Goal | Key Metrics | Actions | Timeline | Insights |
---|---|---|---|---|---|
Healthcare | Reduce patient wait times in the emergency department. | Average wait time, patient satisfaction. | – Streamline triage process. – Add staff during peak hours. | 6 months | Focus on patient-centered care and use data to identify bottlenecks. |
Manufacturing | Decrease production defects by 20%. | Defect rate, production efficiency. | – Train staff on quality control. – Implement automated inspection. | 3 months | Continuous training and technology integration are key to reducing defects. |
Education | Improve student graduation rates by 10%. | Graduation rate, student engagement. | – Offer tutoring programs. – Enhance teacher training. | 1 academic year | Address both academic and non-academic barriers to student success. |
Retail | Increase customer satisfaction scores by 15%. | Customer satisfaction, repeat business. | – Improve staff training. – Enhance in-store experience. | 4 months | Customer feedback is critical for identifying areas of improvement. |
Hospitality | Reduce guest complaints by 25%. | Complaint rate, guest satisfaction. | – Train staff on customer service. – Implement a feedback system. | 3 months | Proactively addressing guest concerns can significantly improve satisfaction. |
Technology | Improve software release cycle time by 30%. | Release cycle time, bug rate. | – Adopt agile methodologies. – Automate testing processes. | 6 months | Agile practices and automation can streamline development and improve efficiency. |
Nonprofit | Increase donor retention by 20%. | Donor retention rate, donation amounts. | – Personalize donor communications. – Improve transparency in reporting. | 1 year | Building trust and relationships with donors is essential for long-term sustainability. |
Feel free to reach out if you’d like personalized guidance on creating a QIP for your organization. Let’s work together to achieve your goals and unlock your full potential!
How to Get Started
If you’re ready to create your own Quality Improvement Plan, here’s a simple framework to follow:
- Identify the Problem: Use data and feedback to pinpoint areas for improvement.
- Set Goals: Define what success looks like and how you’ll measure it.
- Develop Actions: Outline specific steps to achieve your goals.
- Implement and Monitor: Execute the plan and track progress regularly.
- Review and Adjust: Evaluate results and make adjustments as needed.
Proven Strategies for Making a Business Case for Quality Improvement
Convincing stakeholders to invest in a QI Learning Collaborative often involves presenting a strong business case. Here’s how to inspire decision-makers:
- Quantify Impact: Showcase how improving quality will reduce costs and boost revenue (e.g., fewer production errors or increased customer retention).
- Link to Mission: Connect QI goals to your organization’s larger objectives such as, how to improve product quality.
- Leverage Data: Use a sample quality improvement project to illustrate success and learn how to improve data quality.
Improving data quality and product quality is essential for organizations aiming to enhance operational efficiency, customer satisfaction, and overall competitiveness. Below are strategies to achieve improvements in these areas:
How to improve data quality
How to improve data quality
As someone who’s built a multi-million dollar business from the ground up, I can tell you that improving data quality is crucial for making informed decisions and driving success. Here’s what I’ve learned about enhancing data quality in my journey:
1. Establish Strong Data Governance
I’ve found that setting clear standards for how we handle data is key. In my companies, we’ve implemented guidelines for collecting, storing, and using data. This ensures everyone’s on the same page and helps maintain consistency across the board.
2. Invest in Your Team
One of my best decisions is investing in my team’s skills. We regularly conduct training sessions on data quality management. This empowers our staff to handle data responsibly and effectively, which is crucial in today’s data-driven world.
3. Regular Quality Checks are Non-Negotiable
In my experience, you can’t afford to be complacent about data quality. We perform routine checks to catch and fix errors quickly. This proactive approach has saved us countless headaches and potentially costly mistakes.
4. Assign Responsibility
I’ve learned the importance of accountability. In our organization, we have designated data stewards who oversee data quality. They ensure we stick to our standards and continuously improve our processes.
5. Embrace Technology
Finally, leveraging technology has been a game-changer for us. We use automated tools to monitor and enhance our data quality. This not only reduces manual work but also significantly improves our efficiency.
Remember, in business, your decisions are only as good as the data they’re based on. By focusing on these areas, you’ll be setting yourself up for success in the long run.
Improving Product Quality
How to improve product quality
As a business coach and consultant, I’ve seen firsthand how quality can make or break an organization. Quality is the foundation of trust, customer satisfaction, and long-term success, whether it’s the products you deliver, the services you provide, or the data you rely on. Over the years, I’ve developed and refined strategies to help businesses elevate their quality standards. Today, I want to share some of my top insights, tips, and advice to help you do the same.
1. Conduct Thorough Supplier Audits
One of the most critical steps in ensuring quality is evaluating your suppliers. I always tell my clients: “Your quality is only as good as your weakest link.” I recommend conducting thorough supplier audits to assess their capabilities and processes.
- My Advice: Don’t just look at their certifications—dive deep into their quality management systems. Are they aligned with your standards? Do they have a track record of consistency? Use tools like qualityinspection.org to guide your audits and ensure your suppliers are true partners in quality.
2. Enhance Product Design Processes
Quality starts at the design phase. I’ve worked with companies that spent millions fixing issues that could have been avoided with better design practices. The key? Focus on user needs.
- My Tip: Incorporate customer feedback early and often. Tools like insight-quality.com can help you gather and analyze user insights to create products that meet and exceed expectations. Remember, a well-designed product is more straight forward to manufacture, maintain, and deliver at a high quality.
3. Implement Robust Quality Management Systems (QMS)
A strong QMS is the backbone of any quality-driven organization. I’ve seen companies transform their operations by standardizing processes and creating a culture of accountability.
- My Insight: Start by documenting your processes and training your team to follow them consistently. Use resources like insight-quality.com to build a QMS that works for your organization. And don’t forget to regularly review and update your system to keep it relevant and effective.
4. Conduct Regular Performance Testing
You can’t improve what you don’t measure. That’s why I always emphasize the importance of routine performance testing. Testing ensures reliability before reaching the market, whether it’s a product, service, or process.
- My Advice: Make testing a non-negotiable part of your workflow. Use tools and frameworks from insight-quality.com to design tests that align with your quality standards. And don’t just test for functionality—test for durability, usability, and customer satisfaction.
5. Foster a Culture of Continuous Improvement
Quality isn’t a one-time effort—it’s a mindset. I’ve helped organizations shift from a reactive to a proactive approach by fostering a culture of continuous improvement.
- My Tip: Encourage open communication and feedback at all levels of your organization. Platforms like qualitygurus.com offer great resources for building this culture. Remember, your employees are your greatest asset. Quality becomes everyone’s responsibility when they feel empowered to identify and address issues.
Why These Strategies Work
By systematically applying these strategies, I’ve seen organizations achieve remarkable results:
- Improved decision-making through reliable data.
- Higher customer satisfaction and loyalty.
- Greater market competitiveness and profitability.
But the real secret to success? Consistency. Quality isn’t about grand gestures—it’s about the small, daily actions that add up over time.
My Thoughts
If there’s one thing I’ve learned in my journey, it’s this: Quality is never an accident. It results from intentional effort, collaboration, and a commitment to excellence. Whether you’re just starting or looking to take your organization to the next level, these strategies can help you build a foundation of quality that drives lasting success.
Feel free to reach out if you’d like personalized guidance on implementing these strategies in your business. Let’s work together to unlock your full potential and achieve your desired quality standards.
— Ryan Zofay
For example, at We Level Up Health Centers, our early investment in quality and process improvement directly led to operational efficiency, increased ROI, and significant growth. Data points like these win over even the most skeptical executives!
Uniting Through Collaboration
One undeniable strength of QI Learning Collaboratives is the sense of community they foster. Participants not only gain actionable insights—they also build long-lasting partnerships and networks. The shared accountability derived from collaboration inspires participants to think creatively and execute best practices boldly.
Understanding that the continuous quality improvement process is designed to help organizations adapt over time helps create a mindset ready to drive lasting change.
Why Quality Improvement Is Non-Negotiable
Organizations that prioritize quality and continuous improvement gain a distinct competitive advantage. They become more agile, customer-focused, and financially resilient. Through well-designed learning collaboratives, these transformations can happen faster and more effectively than ever.
Implementing QI Learning Collaborative Technical Assistance isn’t just about fixing problems—it’s about purposefully designing an organization that thrives for decades.
Take Action Today
Sign up participants and start forming a quality improvement learning collaborative technical assistance team. Begin identifying areas for improvement. If you’re still unsure where to start, see my free resources on QI implementation for quality improvement learning collaborative. Your quality revolution begins now.
If you’re ready to elevate your organization with these strategies, now is the time to act.
Resources
- Revolutionizing Business Process Improvement through Roundtable Process Improvement Expert Insights
- Uncover How Continuous Improvement is about Evolution not a Revolution
- Free Readiness for Business Transformation Assessment. Digital Business Transformation Guide.
- Powerful business management courses with Ryan Zofay – Entrepreneur & Business expert.
- Top-notch Business Management Consultant Services.
- Ryan Zofay’s Business Coaching Secrets Podcast
- 9-figure Business Masterclass Success Blueprints
- Sanctified Soul Business Transformation with Ryan Zofay To Level Up Your Business & Team
- Must Read Top 25 Best Self Help Books
- Guide to Self Improvement Strategies, Tips, Laws, Setting Goals, Journaling, Courses & Classes