Co-authored and reviewed by Business & Digital Marketing Expert Guy Shapira.
Mastering Business Process Improvement in 2025
Hi, we’re Guy Shapira and Ryan Zofay, process improvement consulting experts who have worked with client organizations to streamline operations, reduce inefficiencies, and drive growth. Whether you’re a small business owner, an executive, or a process improvement enthusiast, we’re here to show you how understanding and applying process improvement can elevate your business to new heights.
This blog will give you insights into what business process improvement is, key methodologies like process mapping and root cause analysis, and how tools like roundtable discussions and fellowships are redefining collaboration in 2025. You’ll leave with clear, actionable steps for applying these concepts in your organization.
Grab a coffee, and let’s deep dive into unlocking the full potential of your workflows.
Our hands-on experience with business process improvement
Revolutionizing Business Process Improvement: My Insights and Guy Shapira’s Expertise
As someone who has navigated immense personal challenges and scaled a multi-million dollar business, I know firsthand the power of continuous improvement. That’s why I’m excited to share insights alongside Guy Shapira, a true leader in business process innovation.
Business Process Improvement
With his experience at various companies across multiple industries, Guy Shapira brings invaluable RPA and AI-driven process optimization expertise. His technical prowess is perhaps unmatched.
On the other hand, my journey has been one of resilience and reinvention. I’ve learned that overcoming adversity requires a relentless commitment to improvement in business and every aspect of life. This perspective has shaped my approach to business process improvement.
Roundtable Discussion
In a recent roundtable discussion, Guy and I explored the future of business process improvement. We emphasized the importance of collaboration and integrating cutting-edge technologies to drive real change within organizations. Our roundtable extended to applying AI for business process improvement deliverables examples and beyond.
Process Improvement Methodologies
We both believe that a mix of traditional and innovative methodologies is crucial. Guy highlighted data-driven decision-making and AI’s potential to identify inefficiencies. I stressed the need to foster a culture of continuous improvement at all levels. Of course, without a team invested in the process, no amount of optimization will produce sustained results. That’s where exercises to take your leadership team on a vision quest can come into play as an initial step to begin root cause analysis and process mapping thereafter.
Process Mapping
Guy shared his expertise on advanced process mining techniques, which provide unprecedented visibility into complex processes. This level of detail allows organizations to pinpoint bottlenecks and optimize their operations more effectively.
Root Cause Analysis
I shared how I’ve used root cause analysis to overcome challenges in my business ventures. Digging deep to understand the underlying issues rather than just treating symptoms has been fundamental to my success. In my discussion regarding the rehab center growth marketing initiatives we undertook at We Level Up, I illustrated our process improvement deliverable examples , from building the right team to applying proper call center handling.
2025 Process Improvement Fellowship
Looking ahead, Guy and I are collaborating on the WLU 2025 Process Improvement Fellowship, a program to develop future leaders in this field. We aim to combine Guy’s technical skills with my inspirational leadership to create a comprehensive learning experience.
How Can You Improve the Collaborative Process
We concluded our roundtable discussion with insights on enhancing collaboration. Cross-functional teams, open communication, and technology are essential, especially in today’s remote work environments.
Our combined expertise offers a holistic view of driving efficiency and fostering continuous improvement.
Resources from RyanZofay.com
To help you implement these strategies, explore these resources on my website:
- Build a Brand in 5 Days: Learn how to quickly craft a compelling brand narrative.
- The Art of Public Speaking: As a public motivational inspirational speaker, author, entrepreneur, and business coach, I often offer personal development seminars and tools to enhance executives’ transformative leadership.
- Online Life Coach Ryan Zofay: Join me to discover strategies to transform your life.
- Personal Development School Classes & Training: Engage in emotional intelligence 2.0 and mental well-being classes.
- Self Improvement Coaching Strategies & Tips: Elevate your self-esteem and self-worth. Begin with complimentary self esteem worksheets to boost confidence and self-image.
- Ryan Zofay’s Breakthrough Coaching Center: Connect with coaches for personal and professional growth.
- Best Life Coaches Videos: Get inspiration and guidance to elevate your life and business.
- Uncover How to Master Your Emotions: A step-by-step guide to emotional mastery.
Jump To
Table of Contents
What is Business Process Improvement?
Are you wondering what process improvement is? At its core, business process improvement is about making processes more straightforward, faster, cost-effective, or aligned with a strategic goal. Whether the focus is improving employee satisfaction, increasing profits, or reducing waste, process improvement starts with analyzing how things are currently done and identifying new ways to achieve better results.
Imagine having a more transparent, efficient system that allows employees to focus on tasks of real value. Process improvement can transform all industries, including manufacturing, healthcare, retail, and tech.
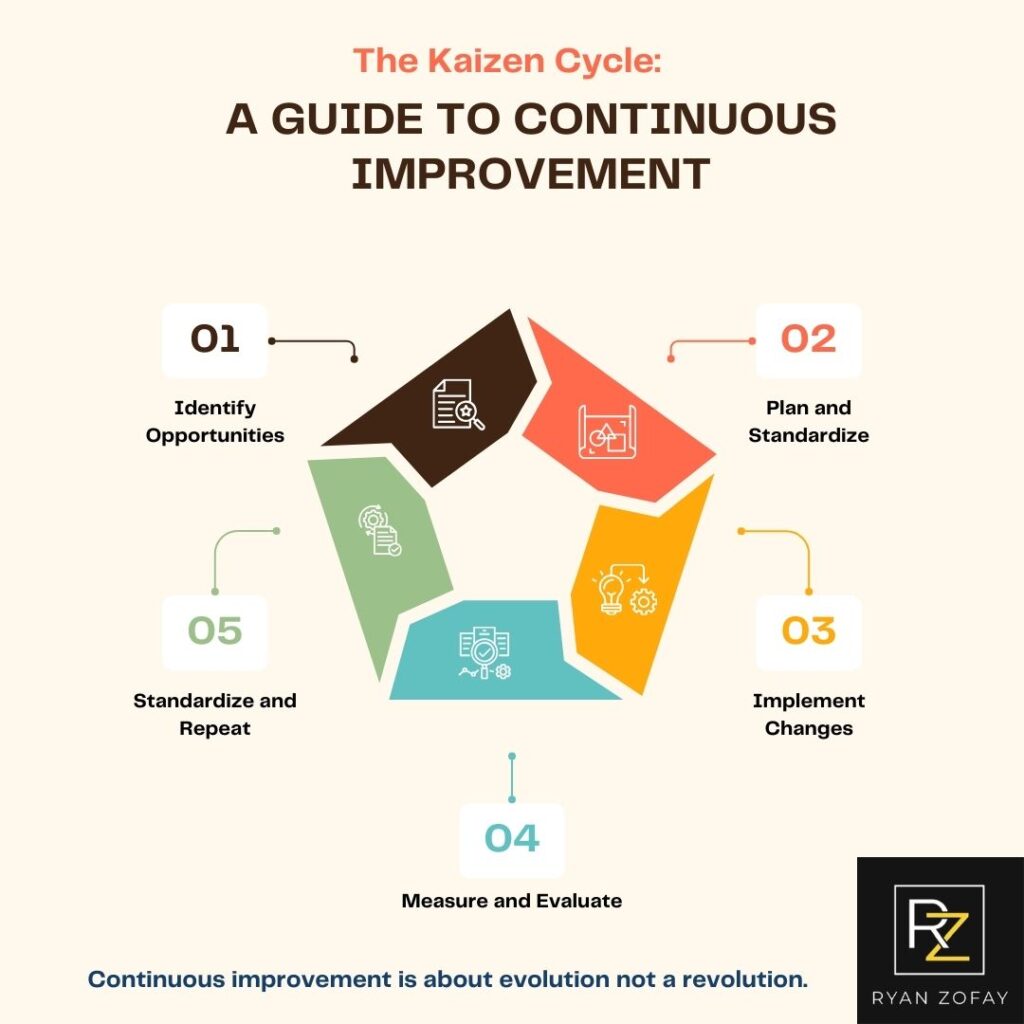
Why Process Improvement is More Relevant Than Ever in 2025
As we’ve worked with diverse organizations over the years, one thing has become clear: the business world doesn’t stop changing. Global trends like AI integration, remote work collaboration, and sustainability have made process improvement crucial. Companies that don’t adapt their workflows to align with these shifts risk falling behind their competitors.
The reality is this—solid workflows prevent breakdowns, even in times of uncertainty. The successful organizations we work with are the ones that invest consistently in their processes.
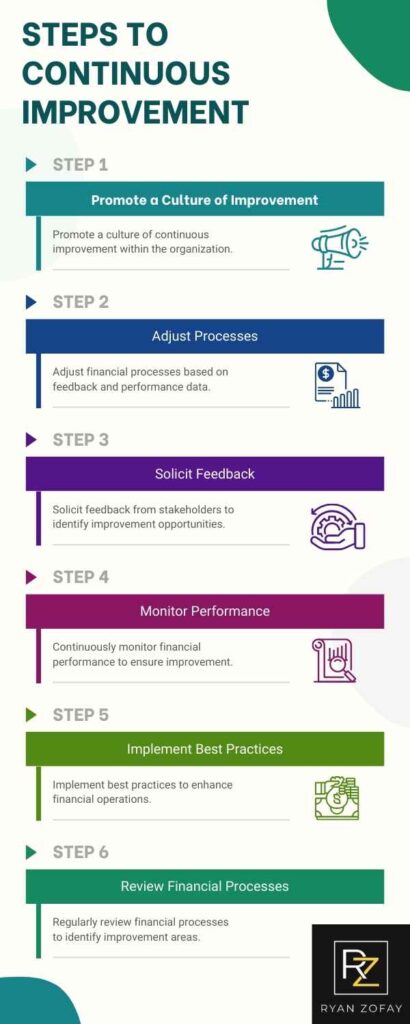
Process Improvement Methodologies That Work
Over the years, we’ve had the privilege of experimenting with and implementing various process improvement methodologies. Here are the top tools we recommend to drive results in 2025.
1. Process Mapping
Process mapping is visually representing every step of a business process. It is similar to creating a detailed “flowchart” of a task or operation.
We can quickly identify redundancies, bottlenecks, and inefficiencies by mapping processes. What looks like a complicated staffing or resource problem often results from poor communication between departments.
Example in Action
A mid-sized software company’s product development team is frustrated by delayed launches. A process map helped uncover that their approval process went through four redundant layers. Streamlining approvals to just two steps saved them weeks of production time.
Quick Tip
Use tools like Lucidchart or Miro to create a process map for your team. Keep it simple! Start with your inputs, the central steps, and the desired outcome.
2. Root Cause Analysis
Not all process issues are apparent on the surface. That’s why root cause analysis is one of our go-to tools. It’s about asking “Why?” until you reach the genuine sources of the problem.
This methodology works exceptionally well with collaborative brainstorming techniques like roundtable discussions.
Example in Action
A retail business struggled with a 20% drop in online customer satisfaction. Instead of blindly investing in more customer service agents, a root cause analysis exposed that their website’s checkout process was overly complicated, causing frustrated users to abandon their carts.
Pro Tip
Use the 5 Whys Technique—ask “Why did this happen?” five times to discover the root cause. Keep digging until you reach the baseline issue that needs addressing.
3. Roundtable Discussions for Collaboration
Speaking of collaboration, roundtable discussions are a tried-and-true approach to breaking silos in any organization. These inclusive forums unite all key stakeholders to collaboratively discuss shared goals and plan improvements.
Our mantra? “The people in the process know the process best.” Empower your team members to bring their unique insights and experiences to the table—it can uncover blind spots and prevent resistance to change down the road.
How Can You Improve the Collaborative Process?
- Provide a structured agenda.
- Keep discussions organized to respect everyone’s time.
- Bring in a facilitator (like us!) to maintain focus.
Roundtable discussions are critical as part of your process improvement methodologies.
Process standardization—where consistency across departments or regions is paramount.
This year will be revolutionary for process improvement professionals thanks to initiatives like the 2025 Process Improvement Fellowship. Here’s why it matters if you’ve heard the buzz but haven’t yet enrolled.
These fellowships offer immersive experiences where business professionals work hands-on with experts to learn and deploy cutting-edge methodologies. Attendees build lasting networks, share tools, and leave with process improvement deliverable examples they can incorporate immediately. From our perspective, it’s where real innovation in our field is happening.
Actionable business process improvement Steps to Get Started
Not sure where to begin with process improvements? Here are small but impactful steps you can implement immediately.
1. Start with a Single Process
Don’t overwhelm yourself by trying to improve every workflow simultaneously. Start with an everyday issue—like streamlining inventory management or accelerating HR recruitment turnaround time.
2. Document Current Processes
Pull together existing workflows in one document. Include key participants, timelines, and dependencies. Add metrics if possible (e.g., “How long does this take today?”).
3. Experiment with Quick Wins
Sometimes, significant improvements don’t require months of heavy lifting. Look for low-hanging fruit—a redundant email chain or an Excel document that can become a shared Google Sheet.
4. Explore Process Improvement and Standardization Services
If your team struggles to manage improvements alone, it might be time to call experts. Consultants (like ourselves) offer tailored services for businesses looking to align decentralized workflows or implement lasting standardization efforts.
Guide to Business Improvement Techniques
Running a business can feel like juggling multiple tasks while keeping everything aligned, efficient, and profitable. Whether you’re a small business owner, project manager, or management consultant, enhancing your processes isn’t just a goal—it’s a necessity. As process improvement consulting experts, Ryan Zofay and I, Guy Shapira, have seen firsthand how refining workflows can drastically transform organizations of any size.
We’ll discuss the most effective business improvement techniques, including process improvement methodologies, examples, and actionable tips you can use today. From understanding the power of standardization to implementing the DMAIC methodology, you’ll find practical approaches to increasing your efficiency and success.
What Are Business Improvement Techniques?
Before we jump into methodologies, let’s clarify the term. Business improvement techniques are proven strategies, tools, and frameworks designed to boost productivity, eliminate inefficiencies, and improve organizational performance.
It’s not about doing more but rather about doing better. For us, it’s a way of achieving your goals and enabling ongoing, sustainable growth.
Why Do You Need Business Improvement Techniques?
No matter how successful, every business has gaps—unused potential waiting to be unlocked. Here’s how well-structured improvement techniques can help grow your business.
- Streamlining Operations: By optimizing workflows, you reduce wasted time and costs.
- Enhancing Collaboration: How can you improve the collaborative process in your organization? Specific processes and methodologies can clear communication channels and ensure alignment.
- Increasing Revenue: Efficiency means delivering more with fewer resources, directly impacting profitability.
- Employee Satisfaction: Better processes lead to less frustration for your team and happier, more engaged employees.
Now that we’re clear on what business improvement techniques, including the “what” and “why,” let’s tackle the “how.”
Process Improvement Methodologies That Drive Results
Business process improvement (BPI) focuses on streamlining operations, enhancing efficiency, and increasing overall organizational performance. Here are some key techniques:
DMAIC Methodology
One of the most effective process improvement methods I’ve used is the DMAIC methodology, which stands for Define, Measure, Analyze, Improve, and Control. This structured approach works wonders for identifying inefficiencies and improving workflows without guesswork.
Breaking Down DMAIC:
- Define – Clearly outline the problem or process you want to improve and set the desired outcome.
- Measure – Collect data to understand the current state of the process.
- Analyze – Dig deep into the data to uncover the root causes of inefficiencies.
- Improve – Brainstorm and implement solutions to address the root causes.
- Control – Put mechanisms in place to ensure the solutions stick and the improvements are sustained.
Many of my clients have been amazed by how powerful (yet simple) DMAIC is when applied to both large-scale projects and smaller day-to-day operations.
Lean Methodology
Lean thinking revolves around eliminating waste, improving value, and keeping things flowing efficiently. A favorite among process improvement professionals, this method emphasizes prioritizing tasks that deliver value and ditching everything else.
Lean Key Tools: Value stream mapping, 5S, Kanban, Poka-yoke.
Focus: Eliminating waste (muda) in all forms, such as overproduction, waiting, transportation, inventory, motion, overprocessing, and defects.
Lean is particularly popular in sectors like manufacturing, but we’ve seen it applied effectively in office settings and even nonprofit work.
Kaizen Continuous Improvement
One of my favorite philosophies, Kaizen, translates to “change for the better” in Japanese. It focuses on incremental improvements over time—a step-by-step approach rather than giant leaps.
Kaizen Focus: Continuous minor, incremental improvements made by everyone in the organization.
Key Concepts: Employee involvement, teamwork, and a culture of continuous improvement.
I love that Kaizen encourages everyone in the business, not just the executives, to contribute ideas for betterment. A quote perfectly captures this mindset: “Great things are done by a series of small things brought together.”
Six Sigma
Six Sigma is revered for its data-driven rigor. Reducing process variation delivers near-perfect outcomes, making it handy for businesses wanting to improve processes where consistency and quality are critical.
- Six Sigma Focus: Reducing defects and variability in processes through data-driven methods.
- Key Tools: DMAIC (Define, Measure, Analyze, Improve, Control), Six Sigma methodologies (e.g., Lean Six Sigma)
Six Sigma capstone projects can deliver genuine process improvement deliverables that exceed client expectations.
Total Quality Management (TQM)
- Focus: Continuous improvement across all aspects of the organization, involving all employees.
- Key Concepts: Customer focus, employee involvement, continuous improvement, and long-term commitment.
Business Process Reengineering (BPR):
- Focus: Fundamentally redesigning core business processes to achieve dramatic performance improvements.
- Key Aspects: Radical change, questioning existing assumptions, and utilizing technology.
Design Thinking:
- Focus: Human-centered approach that emphasizes empathy, creativity, and iterative prototyping.
- Key Stages: Empathize, Define, Ideate, Prototype, Test.
Root Cause Analysis:
- Focus: Identifying the underlying causes of problems to prevent recurrence.
- Techniques: 5 Whys, Fishbone diagrams, Fault Tree Analysis.
Value Stream Mapping:
Focus: Visualizing the flow of materials and information within a process to identify areas of waste and inefficiency.
Process Mapping:
Focus: Creating a visual representation of a process to understand its steps, identify bottlenecks, and improve workflow.
Data Analytics:
Focus: Utilizing data to identify trends, patterns, and areas for improvement.
Tools: Data mining, statistical analysis, business intelligence software.
Automation:
Focus: Automating repetitive tasks to improve efficiency and reduce errors.
Tools: Robotic Process Automation (RPA), artificial intelligence (AI).
Change Management:
Focus: Effectively managing the people side of change to ensure successful implementation of process improvements.
Techniques: Communication, training, stakeholder engagement.
By implementing these techniques, organizations can streamline operations, improve efficiency, reduce costs, enhance customer satisfaction, and gain a competitive advantage.
What About Collaborative Processes?
You’ve probably asked yourself, “How can you improve the collaborative process within my team?” Collaboration is vital to business, but improving it means intentionally creating structures and workflows for better teamwork.
- Establish Clear Roles – Avoid confusion by defining who’s responsible for what.
- Use Collaborative Tools – Apps like Slack, Trello, and Monday streamline communication and task management.
- Foster Transparency – Keep team members informed about processes and decisions for alignment.
I’ve seen businesses transform their teamwork by incorporating straightforward solutions like “stand-up meetings,” which help teams stay updated and aligned.
Process Improvement Examples
Sometimes, the best way to understand the value of these methods is to examine real-world process improvement examples.
- Retail: A small business implemented Lean methodology and reduced inventory costs by 30% by rethinking stocking strategies.
- Healthcare: One hospital used the DMAIC methodology to cut patient wait times by 50%, significantly improving satisfaction rates.
- Tech Companies: A startup applied Kaizen to its product development, rolling out incremental updates that kept users engaged and loyal.
Top 10 Actionable Business Process Improvement Success Tips
Business process improvement (BPI) is essential for organizations aiming to streamline operations, reduce costs, and boost productivity. Whether you’re a small business or a large corporation, implementing the right strategies can lead to significant gains in efficiency and profitability. Drawing on insights from business process improvement consultants, here are 10 actionable tips to help you get started, complete with examples and advice.
Top 10 Tips for Business Process Improvement
Business process improvement involves identifying inefficiencies, optimizing workflows, and creating sustainable solutions for long-term success. Businesses can achieve operational excellence by leveraging proven methodologies like Lean, Six Sigma, and Kaizen. Below are practical tips to enhance your processes, supported by examples of real-world applications.
Tip | Description | Example |
---|---|---|
1. Conduct a Process Analysis | Begin by mapping out your current workflows to identify bottlenecks and inefficiencies. | A retail company uses process mapping to uncover delays in its supply chain and implements automation to reduce lead times by 30%. |
2. Set Clear Objectives | Define specific, measurable goals for improvement, such as reducing costs or improving customer satisfaction. | A healthcare provider sets a goal to decrease patient wait times by 20% through better scheduling practices. |
3. Use Process Mapping | A healthcare provider aims to decrease patient wait times by 20% through better scheduling practices. | A manufacturing firm uses process mapping software to identify redundant steps in its production line, cutting waste by 15%. |
4. Apply Root Cause Analysis | Identify the underlying causes of inefficiencies rather than just addressing symptoms. | A logistics company uses root cause analysis to determine that delayed deliveries stem from outdated routing software and upgrades its system for faster service. |
5. Leverage Proven Methodologies | Adopt methodologies like Lean, Six Sigma, or Kaizen for structured problem-solving and continuous improvement. | A tech startup implements Lean principles to eliminate unnecessary meetings, increasing team productivity by 25%. |
6. Develop a Process Improvement Plan | Create visual representations of workflows to understand better how tasks flow and where improvements can be made. | A financial services firm develops a plan to automate its invoicing process within six months, reducing manual errors by 40%. |
7. Standardize Processes | Establish clear procedures and guidelines to ensure consistency across teams and departments. | A restaurant chain standardizes its food preparation processes across locations, leading to improved quality control and customer satisfaction. |
8. Train Your Team | Provide training on new tools and methodologies to ensure everyone is aligned with the improvement goals. | A call center trains staff on new customer relationship management (CRM) software, improving response times by 50%. |
9. Monitor Progress Continuously | Use dashboards or performance metrics to track the effectiveness of implemented changes over time. | An e-commerce business monitors its website’s conversion rates after redesigning the checkout process, achieving a 15% increase in completed purchases within three months. |
10. Encourage Continuous Improvement (Kaizen) | Foster a culture where employees are encouraged to suggest small but impactful changes regularly, ensuring ongoing optimization of processes over time. | Create a detailed plan outlining the steps to achieve your goals, including timelines, resources, and key performance indicators (KPIs). |
Improving your business processes doesn’t have to be overwhelming if you start with clear objectives and proven strategies. Here’s a quick recap of the actionable steps:
- Conduct thorough process analysis using tools like process mapping.
- Set measurable goals for improvement.
- Leverage methodologies such as Lean or Six Sigma.
- Develop a comprehensive process improvement plan.
- Standardize workflows for consistency.
- Train employees on new tools and methods.
- Monitor progress with KPIs and dashboards.
- Embrace continuous improvement through Kaizen principles.
Implementing these tips, combined with insights from expert consultants and real-world examples, can drive meaningful change in your organization.
By taking these actionable steps and leveraging expert advice from consultants, you can transform inefficiencies into opportunities for growth while fostering a culture of continuous improvement within your organization!
Crafting Your Process Improvement Plan
Here’s an actionable framework you can follow to create your process improvement plan:
- Identify Gaps: Evaluate your current processes. What’s slowing you down?
- Select a Methodology: Pick one that aligns with your goals (e.g., DMAIC or Lean).
- Engage Your Team: Improvement isn’t a solo task. Ensure your team understands their roles.
- Set KPIs: What does success look like? Use measurable outcomes to track your progress.
- Execute and Adapt: Roll out your plan, evaluate results, and refine approaches.
Uncover how Improved Processes Drive Community
Extraordinary business processes trickle down to your staff and customers. They create smoother operations, happier employees, and loyal customers who return repeatedly.
If you’re ready to leap but aren’t sure where to start, we encourage you to join communities or summits—whether through the 2025 Fellowship or other gatherings.
Revolutionary Process Improvement Fellowship Programs
As leaders dedicated to driving innovation and operational excellence, we, Ryan Zofay and Guy Shapira are passionate about empowering professionals to master the art of process improvement. Process Improvement Fellowship is a transformative program designed to equip individuals with the skills and tools to optimize workflows, enhance quality, and achieve measurable results. Whether you’re in healthcare, business, or government, these fellowships provide a structured pathway to becoming a leader in process improvement.
Below, we’ll explore the essential components of a Process Improvement Fellowship, who benefits from it, and examples of notable programs. Let’s dive into how these fellowships can help you elevate your career and make a lasting impact.
What is a Process Improvement Fellowship?
A Process Improvement Fellowship is a specialized program that trains professionals to identify inefficiencies, analyze workflows, and implement solutions for greater efficiency and effectiveness. These programs often incorporate methodologies such as Lean, Six Sigma, Agile, and Kaizen continuous improvement processes. Fellows gain hands-on experience through real-world projects while developing expertise in tools like process mapping and root cause analysis.
Key Components of a Process Improvement Fellowship
Component | Description | Example |
---|---|---|
Hands-on Projects | Fellows work on real-world initiatives to analyze workflows and implement improvements. | Use tools like process mapping, root cause analysis, and performance metrics to inform decisions. |
Data-Driven Analysis | Use of tools like process mapping, root cause analysis, and performance metrics to inform decisions. | A business fellow identifies bottlenecks in supply chains using data analytics, reducing delivery delays by 30%. |
Cross-Functional Collaboration | Engage with teams across departments to ensure streamlined operations and effective service delivery. | Fellows in government agencies work with IT and HR teams to improve employee onboarding processes. |
Professional Development | Training in Lean, Six Sigma, Agile, project management, and change management principles. | A fellow earns Lean Six Sigma Green Belt certification while implementing cost-saving initiatives. |
Mentorship & Networking | Guidance from industry experts and opportunities to connect with leaders in process improvement fields. | Fellows gain mentorship from senior executives at companies like Vizient or Dana-Farber Cancer Institute. |
Who Benefits from a Process Improvement Fellowship?
These programs are tailored for professionals across various sectors:
- Healthcare Professionals: Improve hospital workflows, reduce patient wait times, and enhance care delivery.
- Business Analysts & Consultants: Optimize supply chains, reduce operational costs, and improve customer satisfaction.
- Government & Nonprofit Workers: Streamline administrative processes and improve service delivery for constituents.
Notable Process Improvement Fellowship Programs
Program | Focus Area | Website |
---|---|---|
University of Chicago Medicine QPI Fellowship | Quality performance improvement in healthcare systems | uchicagomedicine.org |
Institute for Healthcare Improvement (IHI) | Leadership skills in quality improvement for global healthcare professionals | ihi.org |
VA Quality Scholars Fellowship | Healthcare improvement research within the Veterans Affairs system | vaqs.org |
Business Process Improvement Office (BPIO) | Performance management and process improvement for city operations | baltimorecity.gov |
Clinical Process Improvement Leadership Program (CPIP) | Care redesign and patient access improvements | dana-farber.org |
2025 Process Improvement Fellowship | Innovative strategies for cross-sector process improvements | wharton.upenn.edu |
Why Invest in a Process Improvement Fellowship?
Fellowships aren’t just about learning—they’re about creating impact. Here’s why you should consider one:
- Real-World Impact: Gain hands-on experience solving real problems within organizations.
- Career Advancement: Develop sought-after skills like Lean Six Sigma certification or Agile project management expertise.
- Networking Opportunities: Build connections with industry leaders who can mentor you throughout your career.
- Cross-Sector Applications: Learn methodologies that apply across industries—healthcare, business, and government.
How to Get Started
If you’re considering a fellowship program but don’t know where to start, here’s our advice:
- Research programs that align with your career goals (e.g., healthcare vs. business).
- Evaluate program components such as duration, location, mentorship opportunities, and certifications offered.
- Prepare by familiarizing yourself with key methodologies like Lean, Six Sigma, or Agile.
Process Improvement Fellowship is more than just training—it’s an opportunity to lead meaningful change within your organization while advancing your career. By focusing on methodologies like Lean, Six Sigma, Agile, and Kaizen continuous improvement processes, fellows develop actionable skills that drive efficiency and innovation.
These programs provide the tools needed to succeed in today’s competitive landscape, whether improving hospital workflows or optimizing supply chains in business settings.
If you’re ready to take the next step in your career or want more information on available fellowships, feel free to reach out! Let’s revolutionize how we approach process improvement together!
Continuous Process Improvement Quotes for Inspiration
Here are some quotes that inspire us as we drive continuous improvement:
- “Continuous improvement is better than delayed perfection.” – Mark Twain
- “If you cannot measure it, you cannot improve it.” – Peter Drucker
- “Kaizen means ongoing improvement involving everyone.” – Masaaki Imai
- “Excellence is not an act but a habit.” – Aristotle
- “Every system is perfectly designed to get the results it gets.” – W. Edwards Deming
Unlocking the True Potential of Your Business
Business improvement isn’t a one-time fix—it’s a mindset. Adopting process improvement and standardization services builds a foundation for scalable growth. Remember, even small changes can lead to remarkable results.
Furthermore, applying business process improvement methodologies isn’t just about reducing inefficiencies; it’s about designing the type of experience people want. From executives tackling bigger-picture goals to employees feeling more in sync, these improvements ripple outward.
If you’re ready to take the first step, start by defining success and being open to exploring innovative methodologies. If you feel overwhelmed, don’t hesitate to reach out. After years in process improvement consulting, Ryan and I have seen how a fresh perspective can make all the difference.
We’re always here to chat and strategize if you’re looking for a roadmap to make it happen and want expert insights tailored to your specific business challenges. We’re here to help you turn inefficiencies into opportunities for success.
Warm regards,
Guy Shapira & Ryan Zofay
Resources
Citations:
- How Continuous Improvement is about Evolution not a Revolution
- Executive Coaching Services. Elevating Leadership Executive Function Skills.
- Business Coaching Secrets Podcast.
- Top-notch Business Management Consultant Services.
- Powerful business management courses
- Power of Transformative Leadership Style
- World Class Top Leadership Development Camp
- Does Servant Leadership Emphasize Coaching?
Sources
Resources for Business Process Improvement
Business Process Reengineering
Process Improvement: Saving Time, Money, and Stress
Process Improvement – Office of Data & Innovation | Salt Lake County
Dive deeper into these strategies and learn more about implementing them effectively: